Post 3 in a series of posts
3) Before we do any gluing of any kind, you’re going to need a couple of things that will save a lot of time. 1) At least 2 strap clamps. 3-4 is optimum ( Home Depot, 14 bucks each) These are really essential. The more you have, the easier the glue up, but 2 will get you done. You can use a tourniquet clamp (which is a rope that is torqued with a lever ( like a piece of broomstick) but believe me, spent the 20-30 bucks on 2 strap clamps. ( You’ll thank me for that advice) Put the clamp on DRY ( with no glue) and slowly compress the shell and examine if the cracks come together and fetch up ( disappear, or form a tight seam) That’s what you want to see at this stage, so you can make a judgment on how and what you’re going to glue up with. ( pic 7) This is a very important consideration! THE GLUE UP IS THE MOST IMPORTANT PART OF THE RESTORATION, PERIOD. The rest is window dressing.
Now at this point of the discussion, I’m going to point out some issues with method and outcome, concerning this project. It deals with overall condition of the drum, and just what you hope to achieve with you’re restoration effort. There are any number of levels you can take it to within reason.
As I mentioned, a good percentage of these vintage drums are beat up, split, or have been repaired. Some of the repairs are good, and some of the repairs are not. I decided that since people on this forum follow the tubs that show up on ebay, (and this was one of the recent ones that was in that loop,) It would serve a purpose to show the restoration of it, and explain in detail what was wrong with the drum upon arrival. Always remember: You cannot tell anything about the real condition of a drum by a photo. This is just a given. On ebay, a basket case still is going to cost you some 150-200 bucks and $35-85 bucks to ship. So we’re talking about 225 minimum unless it’s a local pickup. Now you have a $225 flower pot, that will cost another few hundred to have done professionally ( with varying results) depending on the condition of the shell when excepted. Already you’re up to $500-600 bucks for a used vintage drum. When you do it yourself, you still will be up to $300 overall minimum, when you factor in tools, glues, stains, varnish, new fasteners, metal polish/cleaner , not to mention re- chroming, which will be another $65-100 (or more) It adds up fast. If you pay anything under $100.00 for a vintage Gon bop in ANY kind of condition, you did good!.
Let’s address condition of the shell. There are 3 grades of possible out comes: 1) Museum quality: Perfect in every respect. like new, unblemished. Forget about this happening, unless you have an unblemished shell to work with, with no gouges or x-tra holes, that is in round. It can happen but it is unlikely on average, or you’re going to pay a premium price for it. (I see some nicely done vintage restorations on ebay, going for $450 or more, per drum. That price is not unreasonable, IMO, but nobody seems interested in buying them? Go figure?)
2 A shell in fairly good condition with some splits, gouges, dings, x holes, deep scratches but in round overall Ala old Gon Bops ( pic 10 )
3 A shell that is split and/or split in two, or three, or four, has scratched, dings, dents, gouges, x-holes, took a set and is out of round and beat to shit on top of it. Like most of the drums I buy! ( pic 11)
My intention with this article is to deal with 2-3. #1 is not really relevant to this discussion, but many of the techniques will be the same. I subscribe to the 2 foot rule when it comes to conga restoration. If it looks good from 2 feet away, there you go! If you’re going to take out the jewelers loop, and examine the grain structure, and demand invisible repairs, you better think about buying a new drum, or spent a lot of dough on and old one, with no imperfections.
I would add that if you invest in a vintage conga, or pair of , or set of Drums, and they are in reasonably good shape, ( maybe several splits, and some minor scratches.) You will be able to re-glue the joints, sand the shells, and clear coat them, without having to stain them in order to hide a lot of blemishes that you can’t do anything about. Just follow the glue up procedure, and skip the filling and staining part. Some guys like to hand oil the drum with a rubbing (Tung) oil. If the shell is blemish free, knock yourself out. It’s all good.
Lastly, everyone has different ideas as to what is the best method to do a particular restoration. Mine is just what I’ve found applicable BY HAND and has made me a living for 40 years, in woodworking, without incident, it is just one way of achieving an outcome. Nothing more. This is not the only way to do it, AND I’m keeping it simple to get you to a known quantity, with a reasonably small investment of money, and effort.. it is not aimed at the professional restorer, rather at the handy person with a limited budget who wants to turn out a very respectable looking drum. ( pic 12)
SOME FACTS
All wood ages, expands and contracts, glues dry out, and barrel staves take a set. ALL OF THEM. Small Oak barrels and kegs were probably the first things ( other than hollowed out logs) to be turned into congas. These barrels were available for shipping items to the colonies for centuries. Rum and pickle barrels, nail kegs, etc were plentiful. None of them were ever glued. They were coopered and fitted with iron rings.) They expanded and swelled when filled with liquid, and they didn’t leak! But they all take a set. They conform to their shape over the years and tend to stay that way. ( Folkloric drums traditionally incorporate the barrel rings) Conga shells are no different. Oak and Ash were always the preferred wood because its plentiful, cheap, dense and strong. Mahogany was light, reasonably strong and resonant, attractive and milled well, and was a first choice for cabinet makers. Congas can and are made out of any wood that has good machining properties, and is strong. And attractive, but oak is pretty traditional.
Again, all wooden barrels/ conga shells will take a set. So the first thing you want to check for, before glue up, is whether or not you have a split stave that took a set, OUT OF ROUND.
With the drum being restored here, it had a major end to end split, along a stave, that took a set. (It also had 4 more substantial splits and 8 more minor splits). Well how did I determine that it took an off set? By strap clamping the shell dry, I can examine the severity of the set, and manipulate the shell to see how close I can get it back to the original set, I do this with a simple shop made tool made from a turnbuckle.( about $5- 7 bucks in any hardware store) this little devise will solve a lot of problems. (again I devised this tool out of necessity) someone else probably uses something different.
With the shell compressed fairly hard under pressure, I check to see if there is a visible gap between the staves. This is A VERY IMPORTANT CONSIDERATION. Why? If it won’t pull together DRY under pressure I have a big decision to make about glue choice and alignment concerns.
.
So while it’s compressed, tap it firmly from the inside or outside with a RUBBER mallet. (don’t go whacking it with a steel hammer) if it doesn’t come back to proper set, then put the turnbuckle spreader on the inside of the shell and push it out a little. ( pic 13)
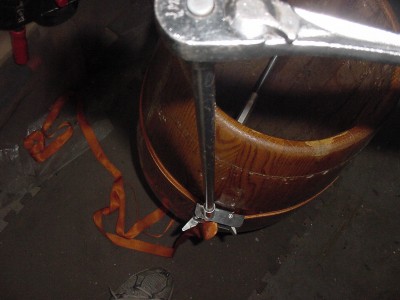
- Dry clamping the shell (pic-7)
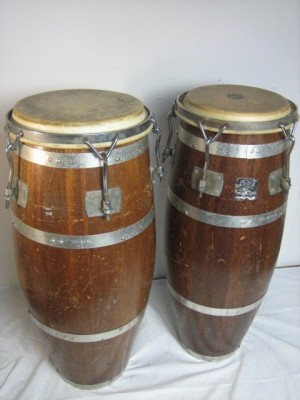
- Typical beat up Gon Bop (pic-10)
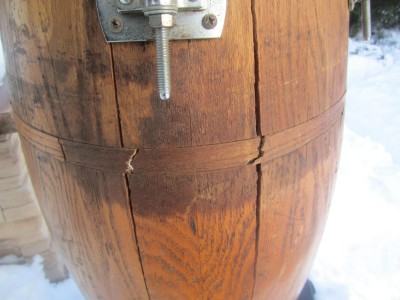
- Typical beat up cracked Gon Bop (pic-11)
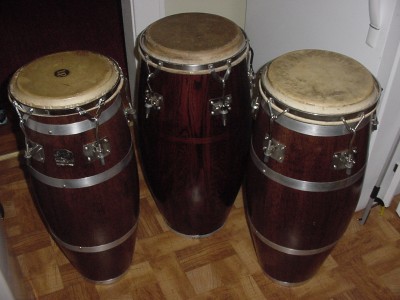
- Restored to playing shape 9pic-12)